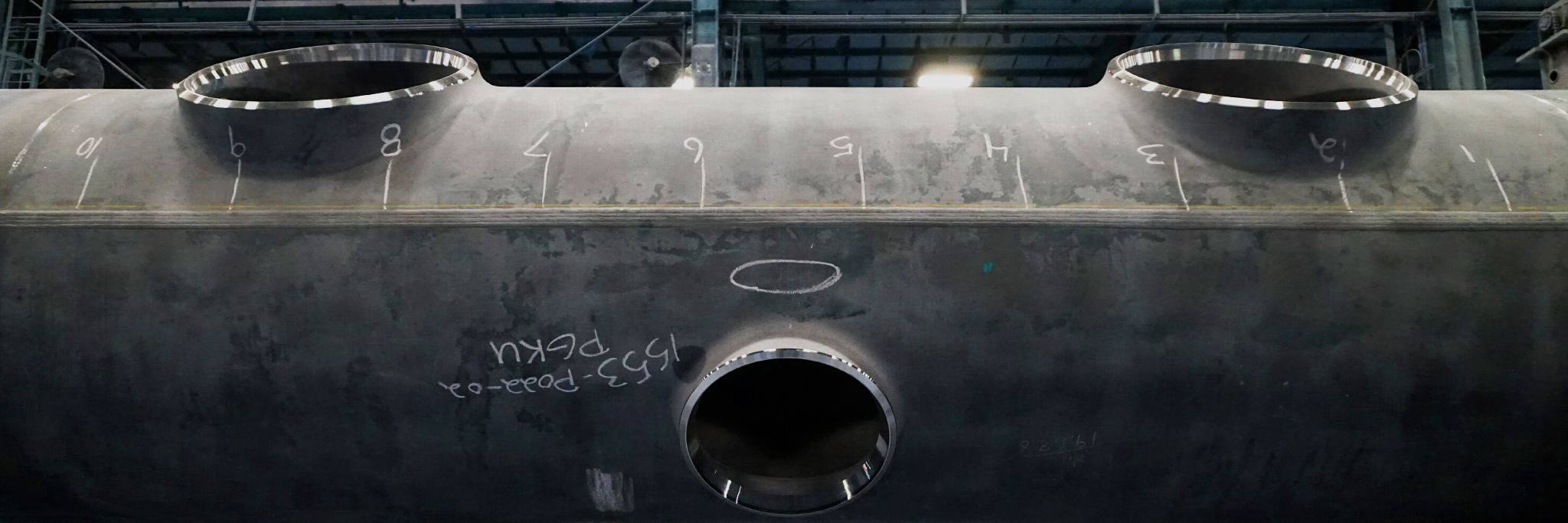
What is an Extrusion?
Taylor Forge Engineered Systems developed the extrusion in the 1950s to fill a gap in outlets that the standard and custom tee couldn’t supply. An extruded outlet is an opening in a cylinder wall made by forming the wall into an integrally reinforced branch connection. It is a low stress self-reinforced connection designed in accordance with code reinforcement formulas. In short, an extruded outlet is more dimensionally flexible than a Tee and more reliable than a welded connection that are typical for pipeline connections.
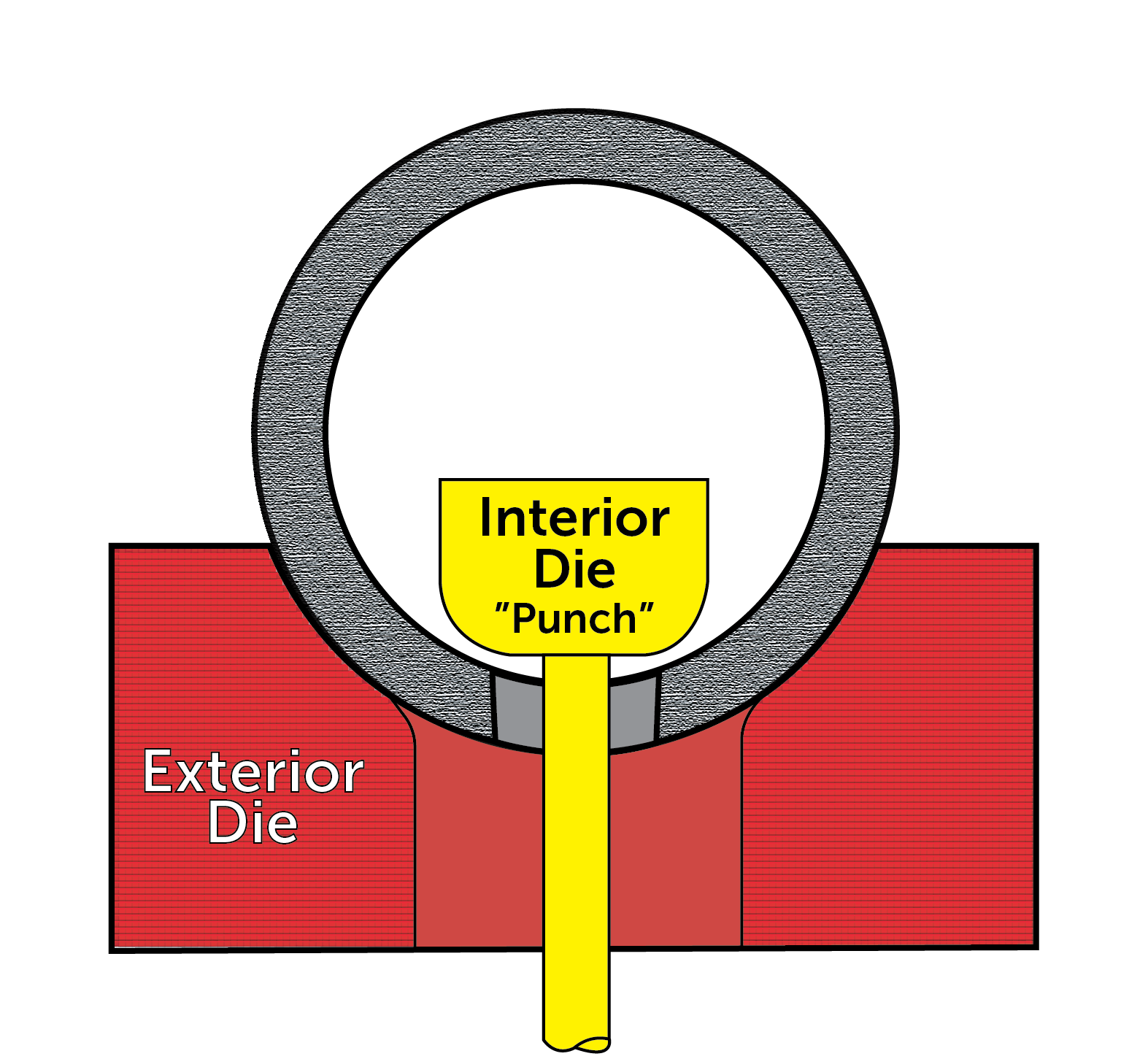
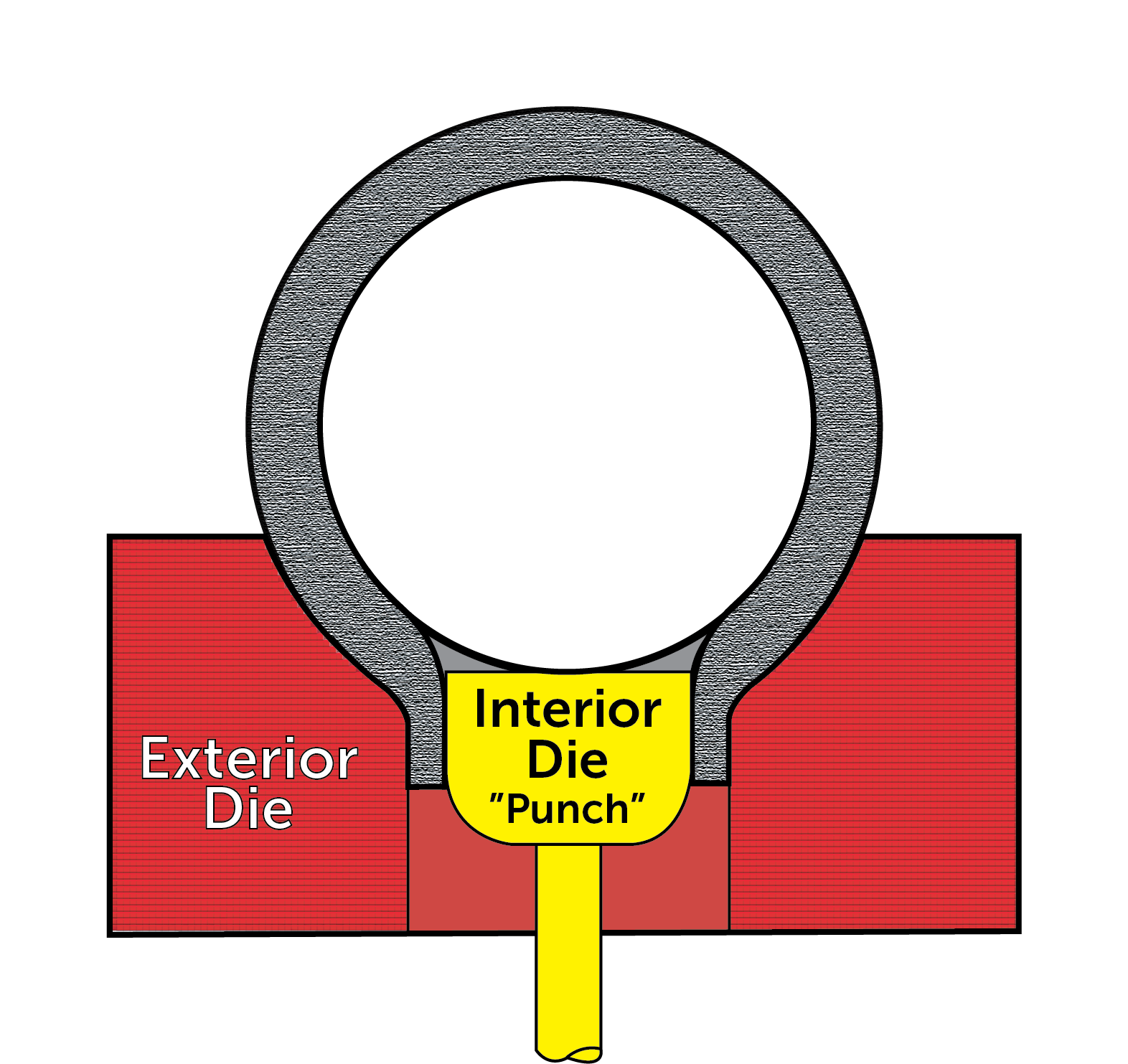
Design Codes
Extrusions can be designed to the Piping Codes – B31.3, B31.8, CSA – Z245.11, or even ASME Section VIII. Formulas within these codes define the material thicknesses required to meet reinforcement code requirements (see fig. 2). Using proprietary internal and external dies, an extrusion supplier will ‘pull’ an extrusion out of thicker pipe that has final thicknesses that meet these specific design codes. The pipeline codes provide a credit in the reinforcement calculations for extruded connections. They also allow for high strength materials. The credit plus use of high strength materials, provides a significant cost savings in many applications when compared to welded or Tee connections.
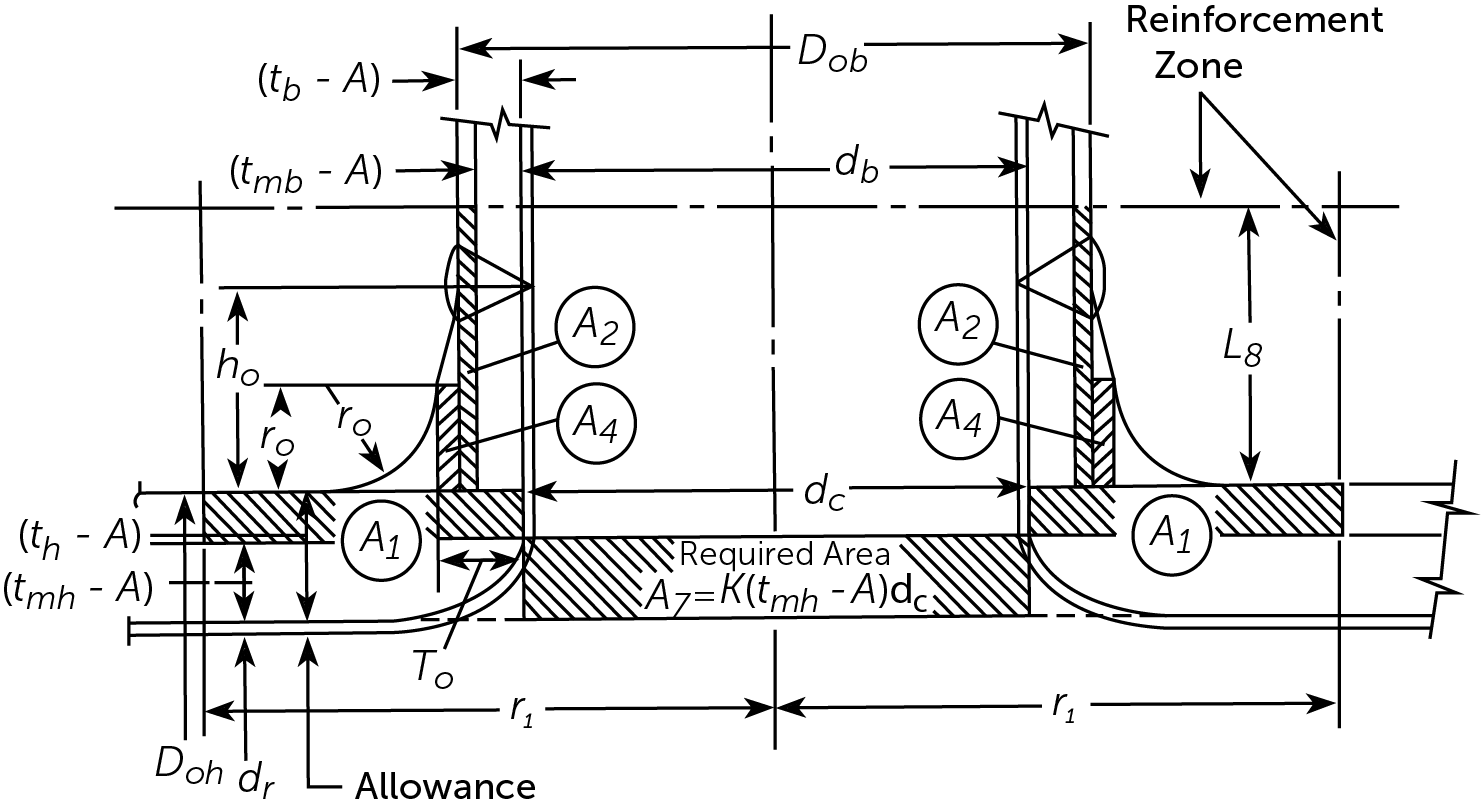
Manufacturing Codes
It is typical for extrusions to be fabricated into a fitting. The fittings will typically fall into MSS-SP75, ASME B16.9, SA/A234 and /or ASME/ASTM specifications. The manufacturing code will define the type of materials and the properties required for an extruded outlet to be considered a fitting per the particular specification.
Layout
Extruded outlets can be designed radially and tangentially along a pipe at any custom distance. The optimal center to center distance is (1) outlet diameter plus 2”. This is the minimum distance to be out of the reinforcement zone of the calculation. If you stay in the reinforcement zone, some additional thickness will be added. Ex: 30” pipe with 8” outlet can be 12” apart. TFES can roll plate up to the 13’ long. The more outlets you can place upon a single run, the more cost effective the design compared to Tees or Welded connections. Extrusions help eliminate girth welds, saving money and time. As with ASME Section VIII, for connections 2” and smaller, no reinforcement is required.
Due to extrusions being pulled out of a pipe or plate run, no size on size connections can be fabricated. This varies from a tee, which can be formed into a size on size configuration. For example, where a 36” outlet is needed out of a 36” run of pipe, we would size up the main run to 38” and swedge the ends.
Quality
Extruded fittings provide a butt-weld, fully radiographable connection. Because of the use of non-heat treated, HSLA (high strength low alloy) plate, extruded fittings can be quench and tempered to meet the final mechanical properties of the site. This versatility allows the manifolds to meet low MDMTs (-50°F) and varying yield stresses (ex: X52,X70, etc) with relative ease.
So you’re on a budget? Check out these 5 tips to save money on your next Slug Catcher Project.
As a leader in Slug Catcher design, here are some guidelines every engineer should know.
Understanding the separation methods for your finger-type slug catcher.
WHY US
Taylor Forge Engineered Systems
has continued the reputation of traditionally dependable products
to a variety of industries.
Integrity
We don’t compromise our practices and we won’t cut corners.