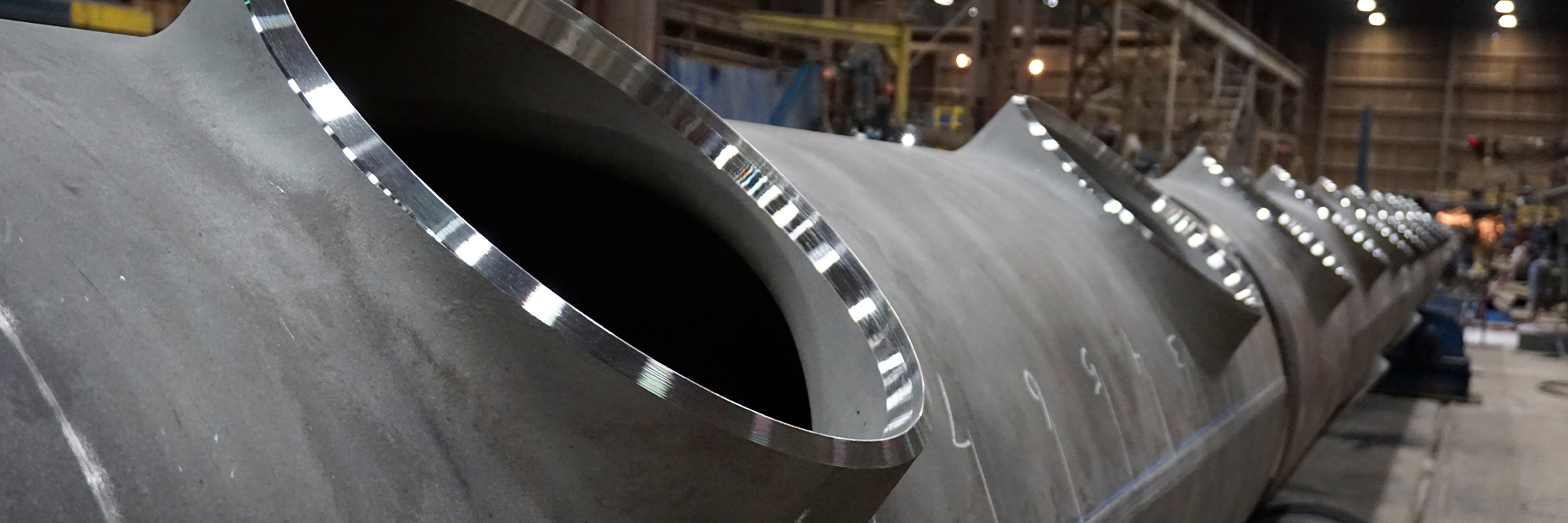
Extrusions fill a void where standard fittings are not sufficient. They are versatile in size, spacing, number of outlets, etc. They are made in a way that their outlets are low stress, fatigue resistant construction. Their applcations utilize many of the specific benefits below:
- They can include tight center to center spacing, minimizing foot print.
- Flexible to your design and manufacturing code.
- The outlet removes the need for pipe and repad and converts this non-radiographable weld into fully radiographable butt welded connection.
- The design can minimize the number of girth welds needed with Tee based manifold design.
- Radial or tangential design or both.
Extruded Tee and Header Applications
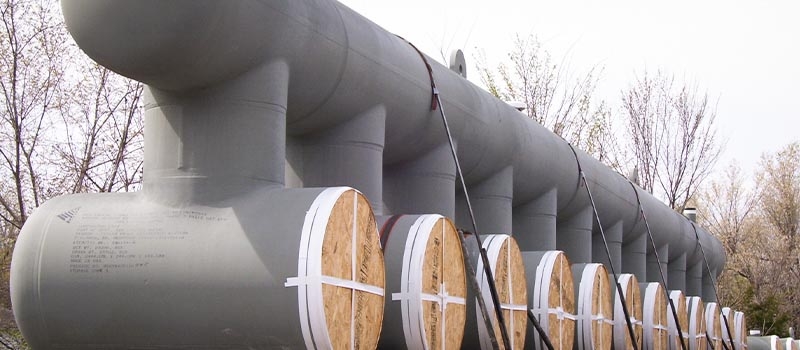
Slug Catchers
Extrusions help reduce footprint and # of welds in a typical harp/finger type unit.
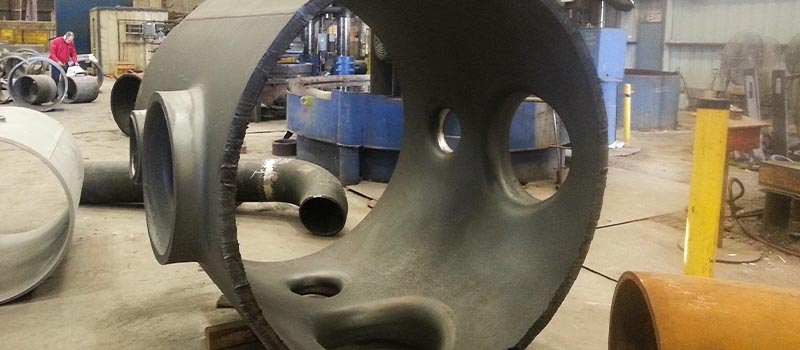
Air Grid Headers
Extrusions allows for numerous circumferential connections on a single cylinder with NO welds. Perfect for high temp and high fatigue applications.
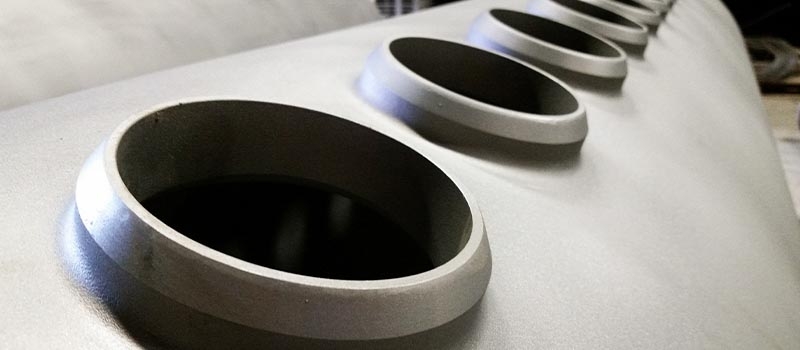
Heater Headers/Manifolds
Extrusions are a higher reliability option for the high temperature and highly fatigued environment compared to welded joints.
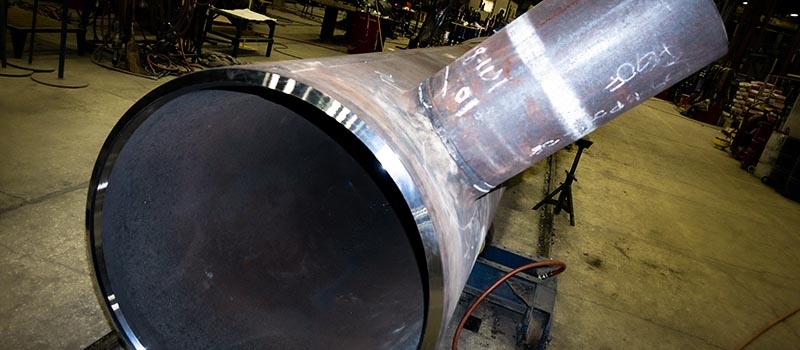
After Cooler Manifolds
Minimizes girth welds, allows for tight center to center spacing, effective in preventing failure in a high fatigue environment. Allows for nonstandard outlet to run dimensions.
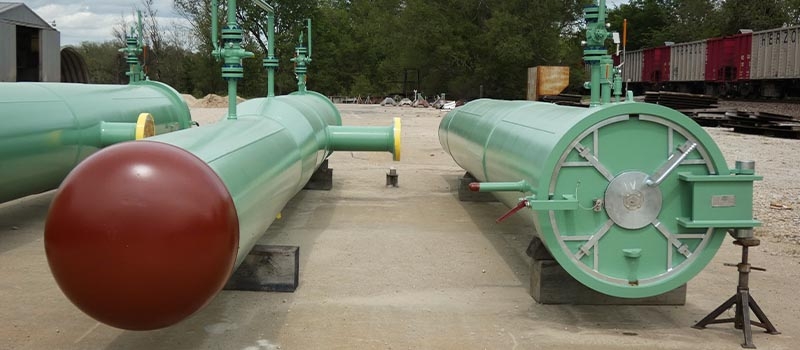
Scraper Traps
The high fatigue ‘kicker line’ joint can be extruded lower likelihood of weld failures.
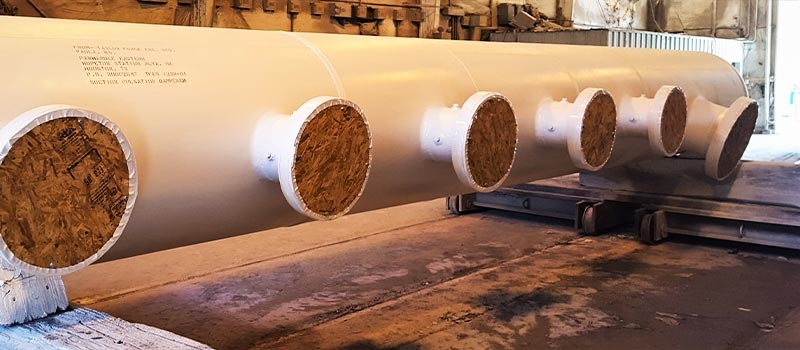
Pulsation Bottles
Ideal for high fatigue/cyclical service environments seen at compressor stations.
Extrusions vs. Tees
Extrusions
- Extrusion is a self-reinforced fitting based on conformance with code reinforcement formula.
- Extruded fittings are flexible with no minimum outlet diameter and additional fabrication allowed within reinforcement rules.
- Initially – Proof Testing.
- Code Case 52 to B31.1 (“K” Factor)
- B31.1, B31.3, B31.4, B31.8
- Additional connections can be added to the fitting after installation.
Tees
- Tee wall thickness based on burst testing data and extrapolation.
- Tees must meet strict dimensional guidelines with one outlet and no other attachments like o-lets, etc.
- Minimum outlet diameter is one pipe size below half of run diameter.
- Can be purchased “off the shelf.”
Extrusion vs. Welding
Extrusions
- Made from a single piece of material
- No welds
- Uniform grain structure
- Resistant to heavy loading and cyclic service
- Limited fabrication required
- Less material than a weld
- No HAZ (heat affected zone)
Welding
- Reinforcement pads are non-radiographable.
- Require greater thickness.
- Create high stress corner joints and exposure to fail in HAZ (heat affected zone).
- More fabrication and material than an extrusion.
- Lower external load factor rating.
- High chance of failure in cyclic service.
Other Technical Articles
As a leader in Slug Catcher design, here are some guidelines every engineer should know.
Choosing the type of Slug Catcher equipment for your next project? This breakdown will help guide your decision.
Understanding the separation methods for your finger-type slug catcher.
WHY US
Taylor Forge Engineered Systems
has continued the reputation of traditionally dependable products
to a variety of industries.
Integrity
We don’t compromise our practices and we won’t cut corners.