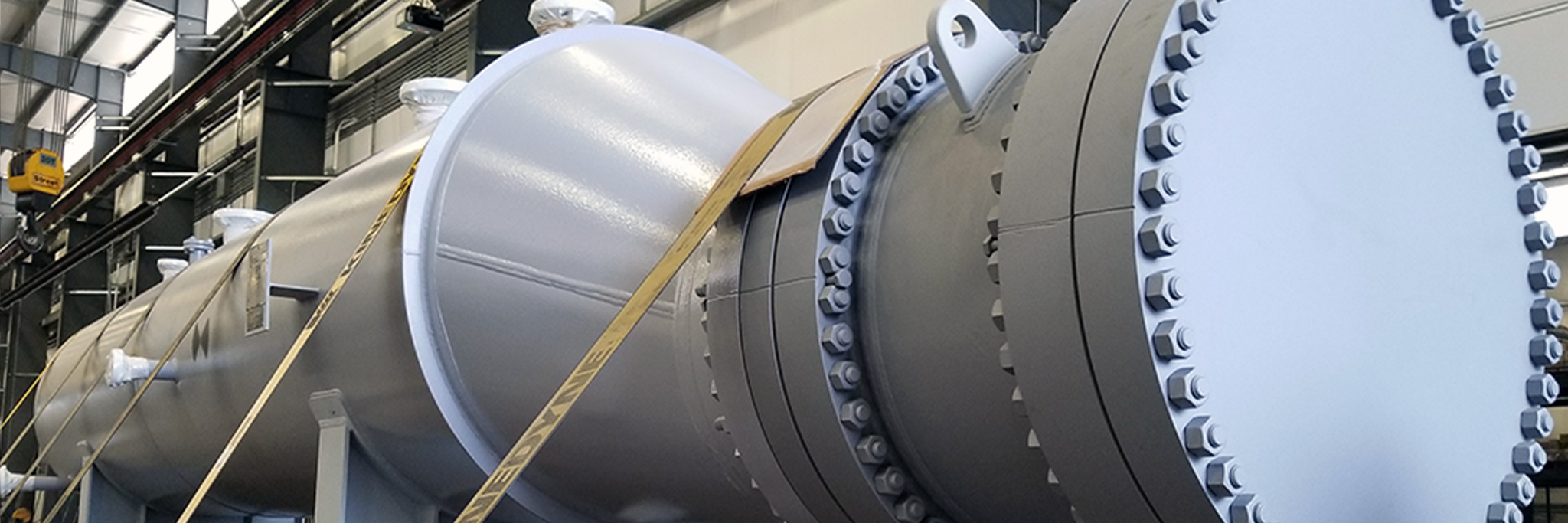
When utilizing a shell and tube heat exchanger for your heat transfer needs, it’s important to consider the operation and maintenance plan as well as budget. The Tubular Exchanger Manufacturer’s Association has defined nomenclature that quickly defines your access to channel, tubes and tubesheet as well as how you perform, maintenance. Below is an outline of these designs.
When we describe the heat exchanger it is in terms of Size and Type. Size is shown as the inside diameter of the shell and the tube length (both in inches or millimeter). Tube length for straight tubes shall be taken as the actual overall length. For U-tubes the length shall be taken as the approximate straight length from end of tube to bend tangent.
Front Head
The front head/channel of your exchanger helps define the access available to the tubesheet, channel, and shell. The A,C, and N types all allow for bolted access to the tubesheet. This means quicker and easier maintenance for tubeside issues. This access makes it ideal for dirty tubeside applications. The C type utilizes an integral channel with tubesheet bolted to the shell allowing bundle removal for dirty shellside applications.
The B-type head is the most common design and lowest cost design. The welded bonnet design is easier to build but more expensive to access for future work.
The ROI of easier access comes at cost that must be weighed first time cost for your facility.
Shell
The most common types are E, K, and F in that order. The rest exist for special cases where you want flows to exit quickly, or have vibration and pressure drop concerns, typically due to high flows.
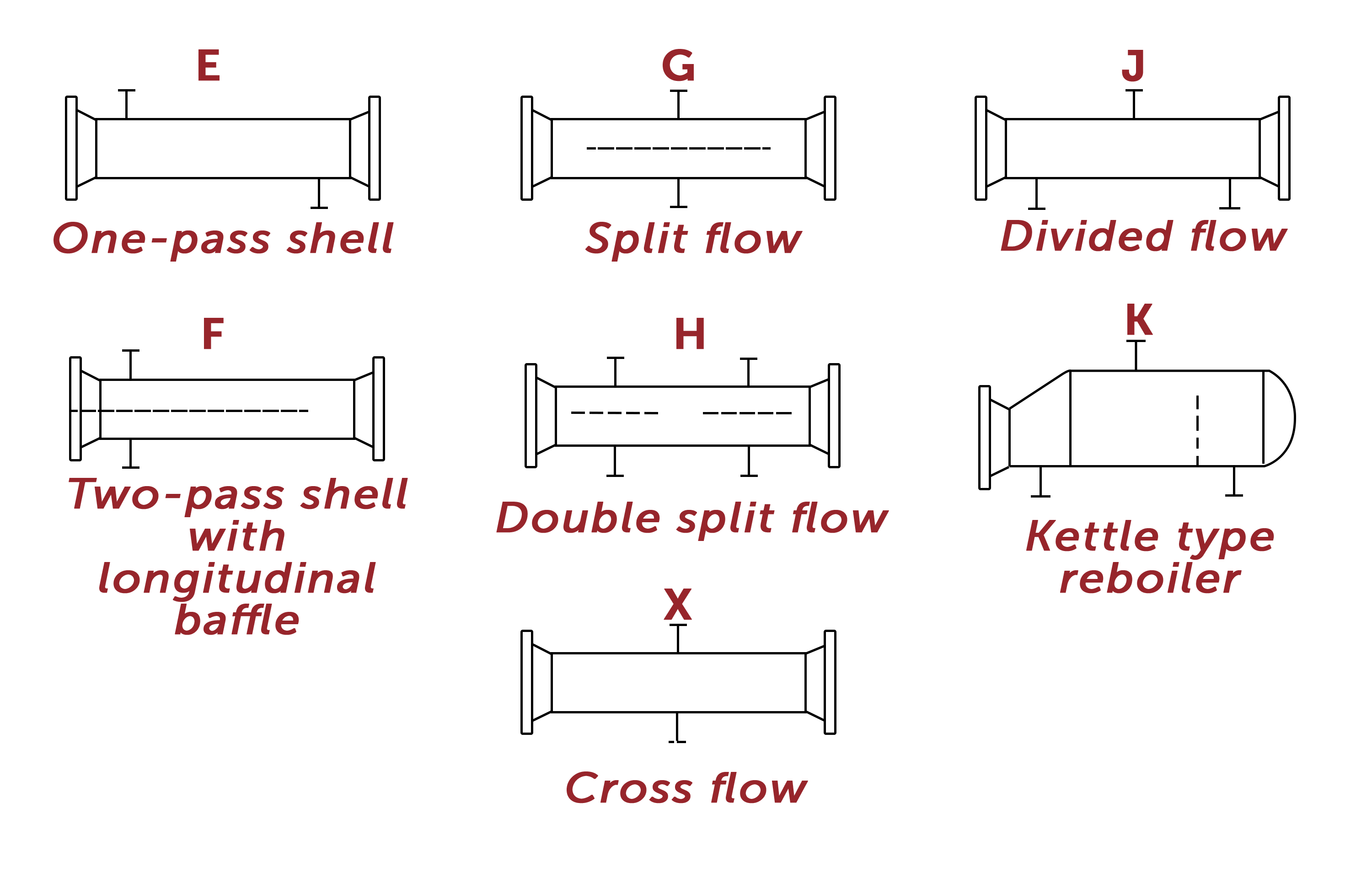
Rear Head
The rear head of the exchanger both defines the access to the back of the bundle, but more importantly, defines if a floating tubesheet and shell head will be used. Depending on different flows, the floating options are better equipped to deal with vibration, corrosion, and other access issues that may occur.
Applying the notes above, you can answer the questions below to pick the right exchanger design for your needs.
- Welded or bolted heads and connections – (Is access or low first time cost more important?)
- Maintenance – (How will you clean or maintain the heat exchangers tube and shell side? Does the process require frequent maintenance?)
- Materials of construction (ex: Carbon Steel is easier to weld than Chrome or SS) – (Is this a corrosive or high temperature process that requires higher grade material?)
- Welding requirements (API 934, API 660, etc) – (Welding requirements can affect pricing in varying degrees depending on the different head/tubesheet connections)
- Crane capacity and freight – (Every manufacturer has varying capacities that make them ideal or less than ideal to handle a project)
For a more detailed look into how the internals of your shell and tube heat exchanger affect your design, please see our other article the discusses baffles, tube pitch, and much more.
Other Technical Articles
As a leader in Slug Catcher design, here are some guidelines every engineer should know.
Choosing the type of Slug Catcher equipment for your next project? This breakdown will help guide your decision.
Understanding the separation methods for your finger-type slug catcher.
WHY US
Taylor Forge Engineered Systems
has continued the reputation of traditionally dependable products
to a variety of industries.
Integrity
We don’t compromise our practices and we won’t cut corners.